Today/Tonight's update:
Cold side is 99% done. The only thing remaining is to get the lugs made that the straps go on - they keep the hose ends from blowing apart. The lugs will go where you see the + on the tubing on either side of the silicone hoses. See 3rd and 4th pic.
First pic, gratuitous up close money shot of the cast aluminum elbow. This was used because the radius needed can't be bent into tubing, so it has to be cast. Luckily, I had some take-offs from a previous project. With some cutting and cleaning, it looked good as new.
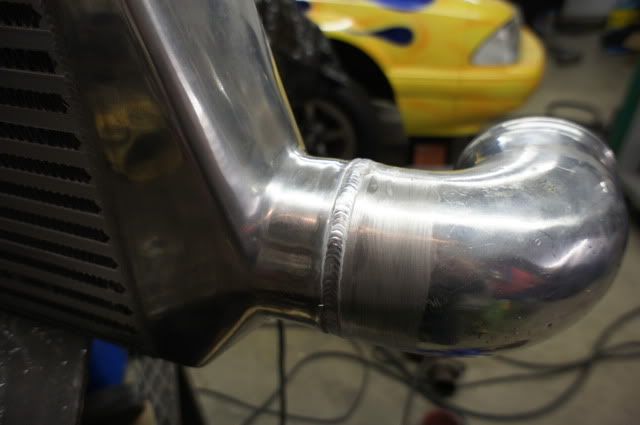
Next, shows where that cast elbow goes, and give you an idea of the space it needs to turn.
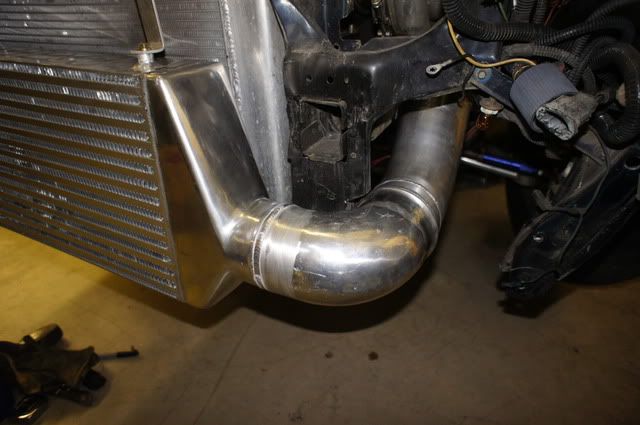
Overall from drivers side above -
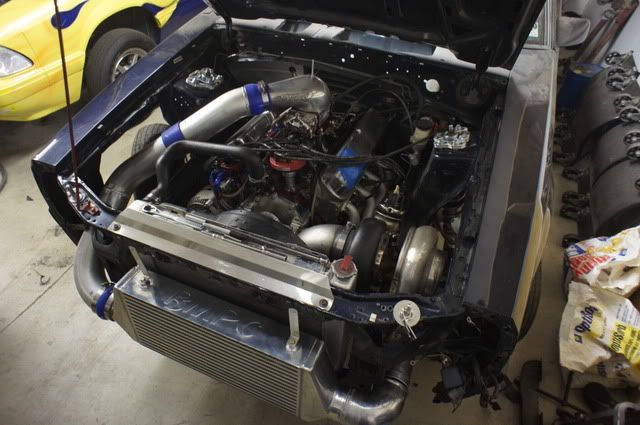
Overall from Passenger side above -
Cold side is 99% done. The only thing remaining is to get the lugs made that the straps go on - they keep the hose ends from blowing apart. The lugs will go where you see the + on the tubing on either side of the silicone hoses. See 3rd and 4th pic.
First pic, gratuitous up close money shot of the cast aluminum elbow. This was used because the radius needed can't be bent into tubing, so it has to be cast. Luckily, I had some take-offs from a previous project. With some cutting and cleaning, it looked good as new.
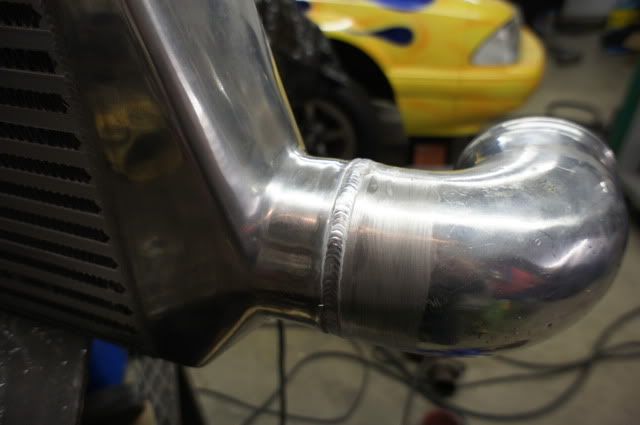
Next, shows where that cast elbow goes, and give you an idea of the space it needs to turn.
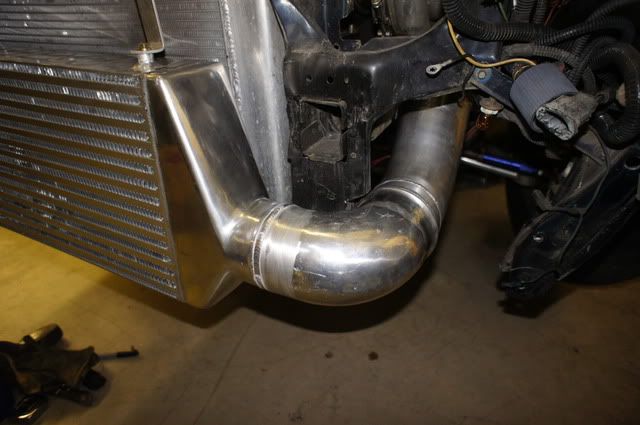
Overall from drivers side above -
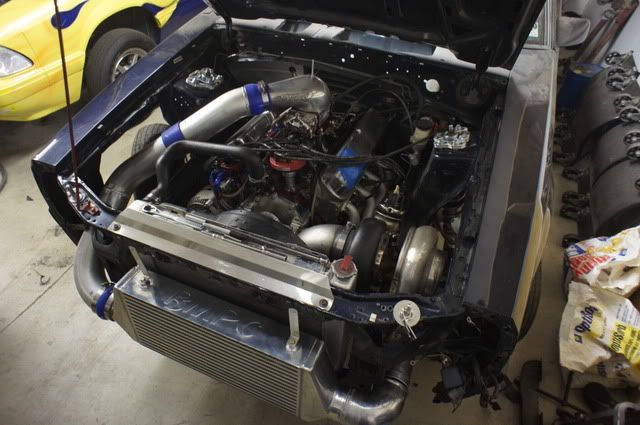
Overall from Passenger side above -
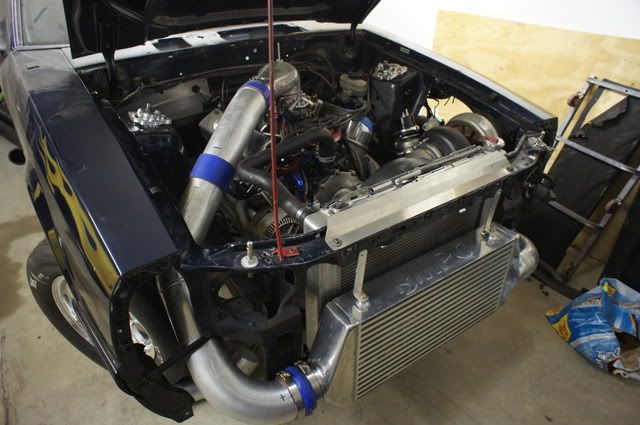
Comment